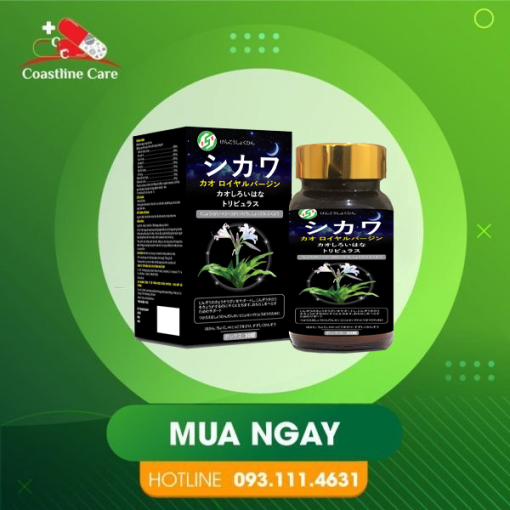
Another challenge is making sure that tasks or adhere to-ups are assigned to the right person or team. In a distant set up, it’s straightforward to overlook who’s responsible for what and to track duties that aren’t assigned immediately. On the other hand, you will discover tools like SafetyCulture (previously iAuditor) that can help with this issue.
These are named soon after Japanese engineering professor Kaoru Ishikawa within the sixties, who assisted use them to producing procedures.
Rate - What exactly are the economic inputs of the method, and What exactly are the fiscal outputs of the process?
Just after graduating, Ishikawa originally served in the Japanese Navy as a complex officer. His tasks included working on chemical weapons and fuel generation, roles that honed his skills in systematic Evaluation and method Manage.
One of several most important difficulties remote groups facial area when conducting root cause Examination is coordinating and communicating successfully. It could be hard, primarily if group members are unfold throughout distinct time zones.
Study producing defects, typical brings about, And exactly how suppliers can apply the most effective practices to forestall faulty products and solutions.
As an Ishikawa Resource and hazop program, SafetyCulture can make it uncomplicated to generate and share checklists, assign responsibilities, and monitor the status of audits or investigations.
One of many humanoid species that wears silver armor and carries a pink pouch. Ponchette no Yoroi-san's pouch was made by himself, and "Chiikawa initially made an effort to buy it at his market place, however it turned out it experienced a leaking gap, so immediately after Hachiware nha thuoc tay pointed it out, he gave Chiikawa a new pouch".
Every single merchandise during the Ishikawa diagrams must be considered as being a hypothesis that may make clear the cause of the failure beneath investigation. A superb speculation really should be very simple and standard whilst nha thuoc tay preventing generating too many assumptions and will be able to make refutable predictions. A less complicated speculation is a lot more prone to be proper.
To stop working (in successive layers of detail) root triggers that likely add to a selected result
Monitoring and checking investigation are similar actions that could be facilitated by copying the Ishikawa products into a spreadsheet such as the a single revealed in Determine 2.
Branching out from the key difficulty, it is possible to develop a procedure map to check various possible will cause. Using a course of action map, you can recognize the gaps as part of your system that nha thuoc tay will lead to your trouble’s root cause.
The 6Ms while in the Ishikawa diagram are vital components accustomed to determine and evaluate troubles in the system. These factors include:
Ishikawa diagrams were popularized in the sixties by Kaoru Ishikawa,[four] who pioneered quality management processes during the Kawasaki shipyards, and in the method grew to become one of the founding fathers of modern management.